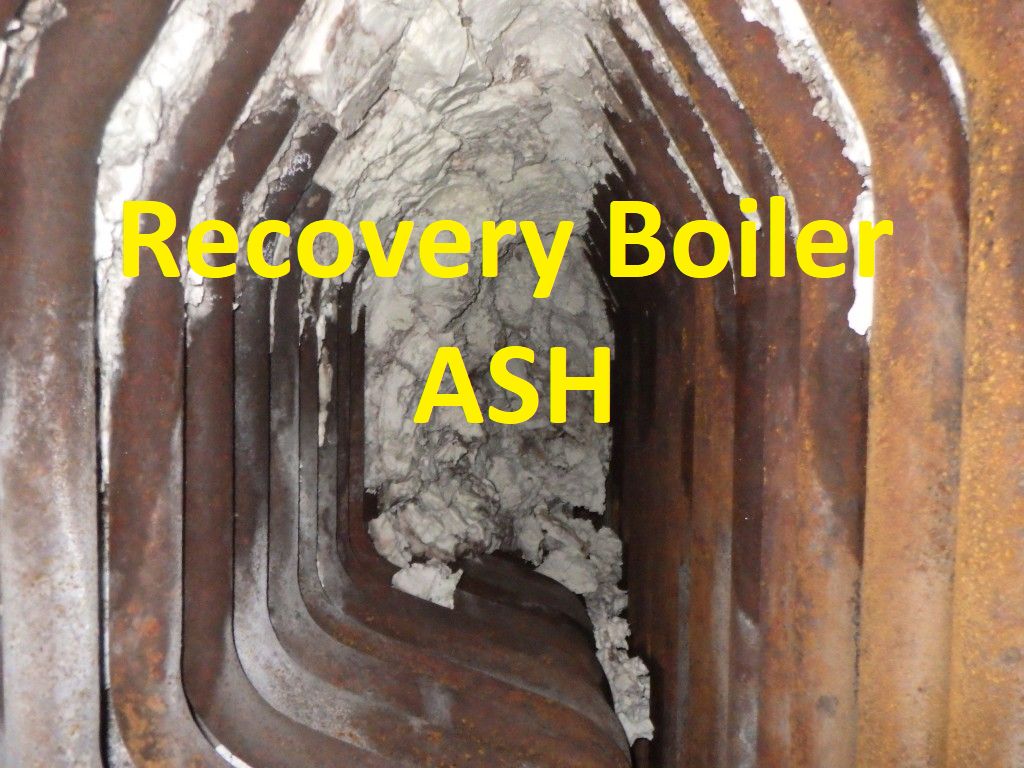
Recovery Boiler ASH - Plugging, Sootblowers, and Ash Induced Corrosion
There is a lot to be said about ash in recovery boilers. If it is under control, everything can run smooth and well. But if it is not, excessive boiler plugging, excessive sootblowing with its own consequences and energy consumption, and even superheater corrosion can occur and make the boiler significantly less efficient or very high maintenance. Let's have a look at this in more detail.
It's all about carryover.
When black liquor is sprayed into a recovery boiler, it needs to be sprayed in such a manner that droplets of the right size are formed and before they hit a char bed, they need to be dry and partially combusted. This condition is achieved by a combination of air flow strategy (air velocities), liquor chemistry, temperature, pressure, and spraying strategy. Boiler tuning achieves an optimal result with the limitations presented by each liquor chemistry or boiler design.
If the droplets are combusted too much by the time they reach the char bed, there is less carbon available for the reduction reaction and reduction efficiency suffers, costing a mill a lot of money. If the droplets are not combusted enough, excessive combustion on the char bed may take place requiring extra air that also has negative effects on reduction reaction.
And if the droplets are so large that they are not even dry when reaching the char bed, the residual water inside the black liquor will impede combustion and cause bed blackout, emission and other problems. All of the above conditions cause reduced boiler performance in one way or another.

Before being sprayed into the boiler, black liquor is heated up in order to achieve a certain viscosity (fluidity). At this point it is sprayed into the boiler under pressure. The viscosity and the pressure dictate how much is the liquor atomized and thus the size and quantity of the droplets. If the droplets are too small (for the air velocities), a substantial portion of the liquor flies upward and becomes what is known as carryover. If the droplets are too large, the liquor drops down onto the bed without much combustion or even drying up and causing reduced reduction and bed blackouts. Again, it is a balancing act between air configuration and black liquor spraying strategy to find an optimal configuration. The picture above depicts this principle of balancing act for liquor viscosity.
As can be seen, it is not possible to completely eliminate carryover without adverse effects on combustion, reduction reaction, and the boiler . The optimal black liquor spraying strategy and thus the viscosity will depend individually on each boiler and black liquor properties in each pulp mill. However, if there is excessive carryover, everything suffers, costing a mill millions of dollars in boiler productivity, energy costs, or make-up chemical costs.
And then, it's also all about liquor chemistry
Now that we have established that it is not possible to completely eliminate carryover, what matters next is the composition of the ash. Why? Because the composition will determine what kind of problems the boiler will encounter. The majority of the ash components are sodium sulfate and sodium carbonate, however there may be many other chemicals such as potassium salts, but also chlorides, sulfides, and others.
It is also important to note that reducing environment will favor creation of sulfides and oxidizing environment will favor sulfates. As such, from the composition of the ash we can deduce the environment. The mechanism of corrosion (in superheaters for example) is also affected by this type of environment - e.g. sulfide vs. sulfate attack. We will discuss this later.
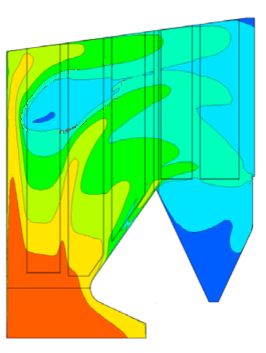
Most of the carryover ash is in a molten liquid phase when exiting the lower furnace. If the liquor is sprayed incorrectly, liquid liquor droplets also join particles flying upwards. Ash then passes through screen tubes, entering superheaters where the flue gas cools down and so does this ash. Liquid ash depositing on tubes may also cool down by the cooler metal temperatures. As the ash cools down it starts to solidify. This doesn't however happen instantly as there are many components in the ash, forming complex mixtures - some forming eutectic mixtures, all melting / precipitating at different temperatures. If all of it is liquid, then the ash simply runs down the tubes - potentially causing corrosion (depending on the composition). Once the ash starts to enter the solid phase, it starts to deposit itself on the surface of superheater tubes and other components. Then the ash continues to cool as it passes further through the boiler components. It has been shown [1] that the ash to be 'sticky', it needs to contain at least 15% liquid phase. This point, designated as T15 is called the sticky temperature. And with further cooling, the ash starts to enter solid state where it remains. The first melting temperature (FMT) is when the solid starts to melt its first components. And remember, the cooling across the superheater is not even, so the actual phase changes and as such precipitation and thus plugging are happening at different elevations for different superheater components. Each superheater also has different steam temperatures adding to the location variability of the precipitation. See the picture above for a modeled upper furnace temperature profile [2].
Potassium
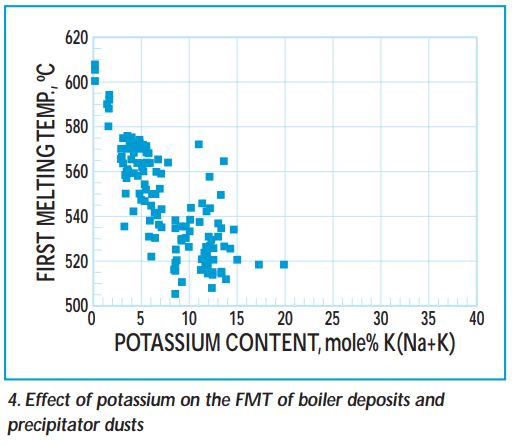
Extensive research has been done [3] showing how the melting temperatures are affected by ash composition. See the picture to the right. The following were the conclusions found in the study:
- Potassium has the greatest effect on lowering first melting temperature (FMT) of the ash
- Carbonates also lower FMT but not as much as potassium.
- For high potassium ash, FMT is decreased as low as 511 degrees Celsius. This has been shown to cause superheater corrosion problems especially if steam temperatures are higher then 480 degrees Celsius.
Chlorides, chlorides, and chlorides...
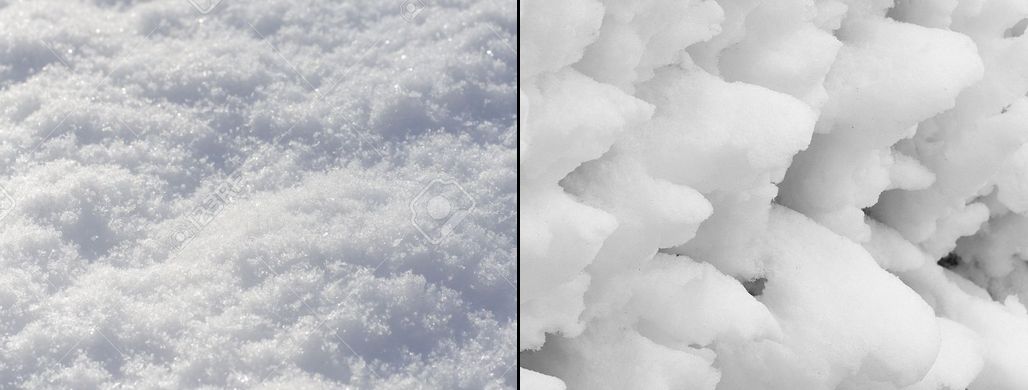
As you can see, composition of the ash affects the melting temperature, which affects the location where the the ash will precipitate and potentially start causing plugging problems.
Now, let's talk about chlorides. The chloride content has a completely different and very significant effect on the ash behavior. Namely, how sticky it is. I have once been advised by a very wise man that there are 3 reasons for boiler plugging. These are: chlorides, chlorides, and chlorides. Chlorides make the ash sticky. Do you know the difference between a powder snow and a sticky snow? Which one is easier to shovel? Chlorides make the ash sticky, and lack of chlorides makes it more 'powder-y'. Picture to the left is from a study [4] made at University of Toronto. The numbers to the right of the picture represent the chloride concentration. As you can see, the higher the chlorides, the more the deposits on the tube.
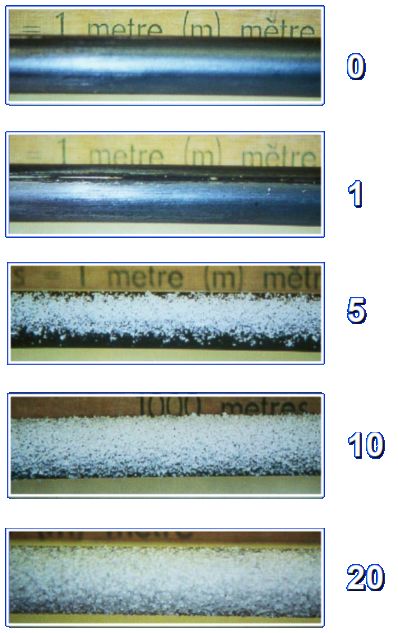
And this brings us to the next topic:
Boiler plugging
Plugging of the flue gas path is a major problem in recovery boilers affecting the production. As the boiler starts to plug up, the area through which the flue gas flows gets smaller and smaller. This causes the ID fan to work harder and harder in order to remove the flue gasses and control the furnace pressure. If this continues, the ID fan can end up running close to its full capacity and unable to effectively control furnace pressure. At this point there is no choice but to shut down the boiler and perform a water wash. Some boilers in the industry are able to run 12 months without this washing while others can barely run for 3.
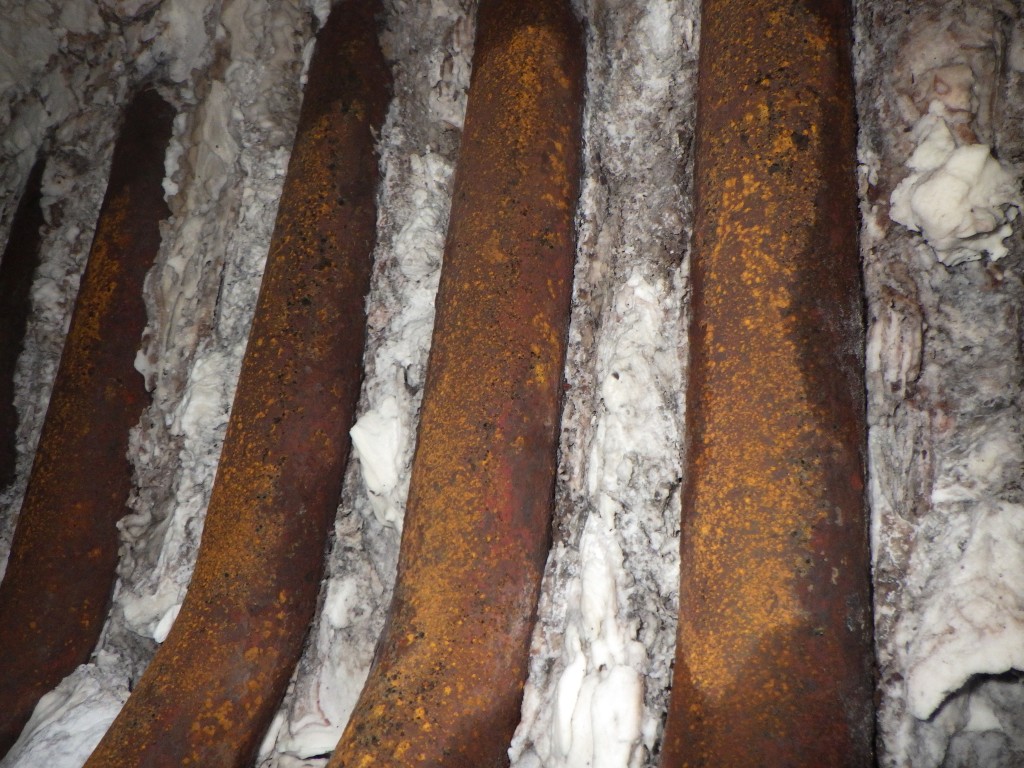
As discussed earlier, there are elements of boiler plugging that can be controlled and then there are those that can't. Adjusting liquor spraying strategy and air flows can reduce carryover. However, if all has been optimized, we are left with limitations that cannot be removed (or at least not without major capital investments), such as liquor chemistry and boiler design.
As discussed earlier, there are elements of boiler plugging that can be controlled and then there are those that can't. Adjusting liquor spraying strategy and air flows can reduce carryover. However, if all has been optimized, we are left with limitations that cannot be removed (or at least not without major capital investments), such as liquor chemistry and boiler design.
At this point, sootblowing is the only strategy to prolong the production before a forced water-washing.
Sootblowing
Efficient sootblowing can prolong the productivity of a recovery boiler significantly. On one side, sootblowing uses energy (steam) that is lost forever and potentially causing erosion and other damage to the tubes. On the other side, they can prolong the productivity of the boiler by reducing the quantity of plugging. Unfortunately, based on our experience visually inspecting recovery boilers, sootblowers are many times neglected. Whether it is routine maintenance or configuration such as poppet valve steam pressure settings. And let's not forget about a major recovery boiler explosion that started by a failed sootblower.
For sootblowing, it is important to direct the sootblowers where they are needed the most. As explained above, the ash will precipitate at different elevations for different superheater sections, depending on the flue gas temperature and the ash composition. At these locations, the plugging will be most significant requiring more frequent sootblowing. Make sure you are using the correct sooblower lance nozzles and the steam pressure is also properly set. The temperature of the steam is also very important as too much superheated steam will not be as efficient. Little things and adjustments can make a big difference.
Superheater corrosion
And last but not least, let's talk about superheater corrosion. Any corrosion is a chemical reaction that grows exponentially with temperature. Superheater tubes are exposed to high temperature environment and are cooled by steam flowing inside. The temperature of the steam also matters as the cooler it is, the cooler the tubes will be. This is why superheaters are often made out of a higher alloyed material in order to withstand these higher temperatures.
If you have a superheater corrosion problem, it can be caused by flue gas environment but also carryover ash. You can address it with any of the following action steps:
- Investigate the type of corrosion products and change the environment (e.g. from reducing to oxidizing - liquor spraying and air strategy adjustment)
- Better control of carryover ash
- Lower the temperature of the steam (this also lowers the efficiency of the thermodynamic cycle)
- Lower the temperature of the flue gas (this may lower efficiency or production)
- Upgrade metallurgy
What kind of corrosion is present in the superheaters depends on the flue gas and ash composition. It might be as simple as oxygen corrosion on lower alloyed carbon steel tubes at high temperatures. However, it could also be as complex as sulfide stress cracking, sulfidation attack, or molten sulfates corrosion. All of this depends in what chemical form (reduced or oxidized) the carryover ash deposits itself onto the tubes and at what temperature. A proper metallurgical analysis of the corroded tube can identify the mechanism of the corrosion upon which proper steps can be taken.
Boiler tuning
Each recovery boiler is unique and each pulp mill has a unique black liquor. Boiler tuning can however provide optimal operational and configuration strategies that increase productivity and decreases operational and maintenance cost. Little adjustments in the right direction can make great impact. And save millions.
If you exhibit any of the problems described above, call us now: +1 877 671 0703.
References
[1] - The sticky temperature of recovery boiler fireside deposits (2002) - Tran, Mao, Kuhn, Backman, Hupa
[2] - An integrated study of flue gas flow and superheating process in recovery boiler using computational fluid dynamics and 1D-process modeling - Kumar, Maakala, Vuorinen
[3] - Effect of composition on the first melting temperature of fireside deposits in recovery boilers (1999) - Tran, Gonsko, Mao
[4] - Overview of Factors Affecting Fouling in Recovery Boilers (2003) - Honghi Tran