
Smelt Spout Failures - And Prevention
Smelt spouts are an integral part of a recovery boiler operation, aiding in the removal of the molten smelt from the lower furnace and safely directing it to the dissolving tank where it dissolves into a green liquor. This system includes many other elements including the entire dissolving tank system, but in this article we will focus on the smelt spout and its cooling system only. Additionally, we will also only focus on critical operation parameters that extend the spout lifetime.
Smelt spouts have a limited lifetime and that is due to thermal stresses but also erosion effect of the smelt flow during an operation. Molten smelt exits the recovery boiler at a temperature as high as 850 °C (1500 °F). So not surprisingly, the smelt spouts are under a lot of thermal stress. Many times, it is exactly those smelt spouts that are the bottlenecks in how long a recovery boiler can run, and at other times, it is those same spouts that bring the boiler down unexpectedly. So, let's have a look at them.
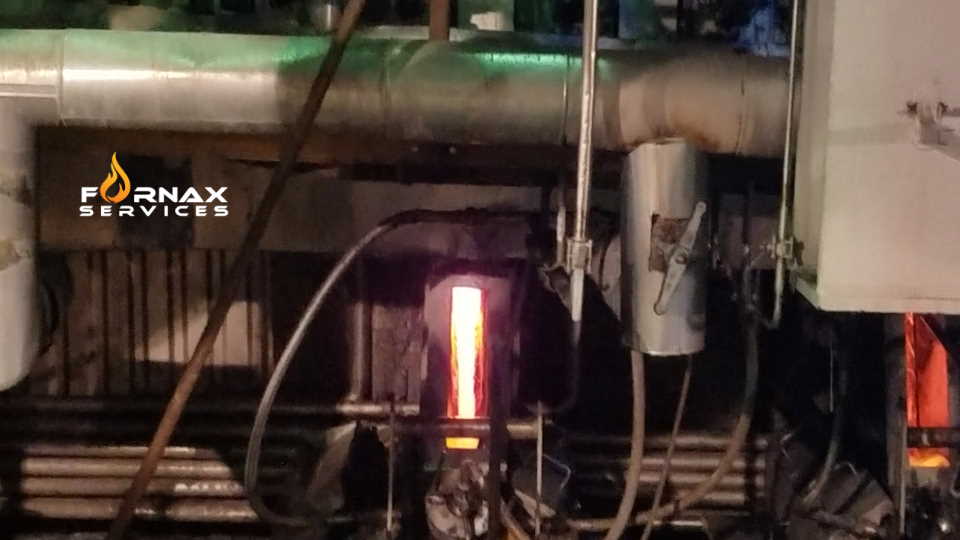
Types of Smelt Spouts
Due to the high temperature of the molten smelt, the spouts have to absorb and withstand a lot of heat. As such, the spouts are categorized by how they are cooled:
- Pressurized water cooled spouts
- Vacuum water cooled spouts
- Non water cooled (dry) spouts
The most common are pressurized and vacuum water cooled spouts with the latter being the most dominant in the newer boilers.
Operation
Cooling Water - Quality
Water cooled spouts need a reliable and constant source of water. Due to the very high heat absorption rates, the quality of water is very important and it should come from steam condensate or a demineralized water. Any solids in the water WILL deposit inside the spout cooling jacket, slowing down the heat transfer, and eventually overheating the material and leading to a spout failure - unless it is replaced by a scheduled maintenance before it happens.
Many mills claim to have exactly this system, yet they have many deposits inside their spouts. This is due to a make up water, an emergency water, or "reserve water" that intermittently enters the system due to certain conditions (e.g. low tank level, or low spout flow) and contaminates the water cooling system. All of this water needs to be a high quality water.
Additionally, the cooling water should be chemically treated to minimize deposition and corrosion.
Not following any of the above conditions WILL decrease the lifetime of the spout in operation.
During your each annual shutdown, pick one of your spouts, and have it cut open so the water jacket can be inspected for deposits. See the above pictures.
Cooling Water - Temperature
Temperature is another important factor for the spout lifetime. Even if the water quality is excellent, and for all sources of cooling water, the spout can still fail due to improper water temperature. How is this?
If the temperature is too low, it may cause condensation of fumes from the dissolving tank at the lip of the spout, causing an external corrosion and ultimately failing the spout (leaking water jacket). The minimum water temperature entering the spout should be followed as per the manufacturer but the industry recommends it to be no less than 60 °C (140 °F).
And if the temperature is too high it will cause boiling of the cooling water, disrupting the flow and along with it the heat transfer, leading into the spout overheating and its failure. The temperature should be kept below the boiling point with a margin, just in case there is a smelt run off which will cause cooling water temperature to rise. And remember, for the vacuum water cooled spouts, the boiling temperature depends on the pressure of the vacuum and is significantly below 100 °C (212 °F). Industry recommends a maximum exit temperature of the cooling water to be no more than 82 °C (180 °F).
High temperature alarms should be setup to indicate temperature approaching boiling point and this should account for the actual water pressure in the spout. Low temperature alarms should be installed as well. Temperature elements should be installed on each individual spout along with all alarms.
Cooling Water - Flow
This may sound obvious but without a flow there is no cooling, and at temperatures of molten smelt, it does not take a long time to damage a spout if it is not being cooled. This is why a spout needs to be taken out of service if its cooling water has been shut off, even for a short period of time - for example to check a source of a leak (see dissolving tank explosion case study article).
If a spout cooling water was interrupted, for any reason, do NOT restore this cooling water. The spout needs to be taken out of service. If a recovery boiler can operate without this spout, install a spout plug, and schedule the spout for replacement during the next shutdown. If the spout is required for operation, shut the boiler down, and have the spout replaced.
Water flow can be interrupted for many reasons, such as loss of a pump, loss of a vacuum, obstruction in the flow, boiling of the water in the spout jacket and others. For this reason, a low flow element should be installed in each spout outlet and a low flow alarm should be activated if such a condition occurs.
The recommended flows (and alarms) depend on the spout heat loading and should be followed by manufacturer's recommendations. It is not unusual for these flows to be 2.5 to 3.8 l/s (40 - 60 gpm).
Cooling Water - Pressure
The pressure affects the boiling point temperature, however outside of that it is only important if the spout actually starts to leak. In such a case, it is not desirable for the cooling water to enter the lower furnace or come into contact with the smelt - or tubes. As such, the pressure should be as low as possible. For the vacuum water cooled spouts, this pressure is below atmospheric which is the safest system. However, even with these systems, we have experienced water splashing out of the spout jacket and causing cracking on one of the spout opening tubes.
Cooling Water - Conductivity
For a vacuum water cooled spouts, a conductivity sensor is recommended to be installed on each spout outlet cooling water line for an early detection of a spout failure. If a spout leaks, it will draw in molten smelt which will increase conductivity of the cooling water. An alarm should be set up for such an incident.
Design
A few design and miscellaneous suggestions:
Isolation valves for each spout should be clearly labeled and operators should be familiar with these. This is to prevent shutting off a cooling water to a wrong spout in emergency situations. Additionally, all of these shut off valves should be installed at a safe location and thus not on a spout deck.
When replacing a spout, they should be field hydro tested to manufacturer's specification prior to use. It is NOT recommended to rebuild or repair a smelt spout.
If you are experiencing spout failures (or cracking) despite no operational issues described above, check the manufacturer's recommendation for the spout loading. Many spouts are designed to process smelt flow produced from 500 tons/day of black liquor dry solids (1.0 MM lbs/d d.s.), some run up to 650 t/d (1.3 MM lbs/d). However remember that if your boiler is designed for e.g. 2,500 t/d d.s. (5.0 MM lbs/d) and you have 5 spouts, these spouts may not be equally loaded, and some may process 350 t/d d.s. and others 750 t/d d.s. and thus failing.
On average, 1 kg of dry solids black liquor will produce about 0.4 kg of smelt.
Dry Spouts
We have not given too much details about dry spouts. Dry spouts do not require the cooling system making the operations easier - at a cost though. It is reported that they require more attention (cleaning and clearing the solidified smelt) during the boilers start-ups or upsets, as these are not warmed up and causing the first smelt running through to solidify. If the spout does become plugged, it may increase smelt flow through other spouts causing excessive wear.
The service life is not being reported to be higher than water cooled spouts and is heavily dependent on smelt condition, temperature, black liquor loading, and spout maintenance. As such, replacement cycle is very site specific.
Latest Technology
Several manufacturers reported to have a spout that is able to restrict smelt flow. This is e.g. important during heavy smelt run-offs potentially causing a dissolving tank explosion. See some case studies here. Customers have not however reported a great success with these yet. This technology is under development. Let us know if you'd like more information.
Spout deck is one of the most dangerous places around a recovery boiler. Yet operators are required to come here often and manually clean the spouts. Full gear protective equipment is required to be at the spout deck. Multiple manufacturers offer automatic spout rodders or robotic spout cleaners. We know of these from Andritz, B&W, and Valmet. Let us know if you'd like more information.